DIY board dryer
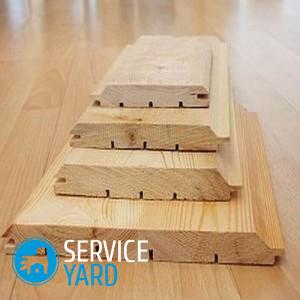
If you have a large amount of unprepared wood that needs to be dried soon, you need to get a special dryer to perform the primary processing of the material. This is an obligatory procedure during construction and finishing work, since if the material is raw, then there will be problems with its installation, and in the future other construction defects will appear. You will learn how to make a board dryer with your own hands from this article.
to contents ↑Bit of theory
Before proceeding with the manufacture of such a structure, you need to find out why you need to dry the tree. From the name it is clear that the design is designed to get rid of excess moisture from wood, however, you need to dwell on some theoretical points.
Wood moisture
Wood moisture is divided into two groups:
- Free, that is, located in the cell cavities and intercellular space. The content of this moisture group is determined by the conditions under which a particular tree grew, as well as by how the sawn blanks were stored. During drying, such moisture evaporates quite quickly.
- Bound or structural moisture - the so-called liquid, which is part of the cell walls of a tree. The amount of structural moisture depends on the type of wood - this means that the drying length can vary: trees, depending on the breed, can get rid of the bound fluid for several months or several years.
Important! Typically, a tree is not more than 30% saturated with moisture. Rocks with a high moisture content are called “gray”, and are usually not used in construction.
What is drying for?
Before you make a drying chamber for wood with your own hands, you need to decide what it is for. We will carry out a small analysis and answer this question:
- When moisture is removed naturally, the configuration of the wood fibers changes, which is why the dimensions of the board are reduced.
- At the same time, the board loses excess moisture unevenly, which is why deformation of completely different planes and at different speeds occurs.
- Due to the uneven “drying out”, so-called stress lines are formed inside the workpiece, giving rise to cracks.
Important! Usually the board gives a crack along the fibers, originating from the end. This happens due to the fact that in these places the bonds between the longitudinal fibers are somewhat weaker.
- Another problem is the lateral deformation of the board - the part takes on a completely unusual shape, arched by an arc or “propeller”. This is due to the fact that the fibers dry unevenly and not simultaneously, therefore, their length decreases, also differing from each other.
Important! From the above facts it is clear that wood with a high moisture content during poor drying can become worthless. You can get away from this problem by preparing the raw materials and drying them on a self-made wood dryer.
Three drying modes
When you use drying chambers, you significantly save the time required to prepare the material for work. Moreover, you can control the drying regimes by controlling the operational properties of wood. At the moment, there are three modes of tree dehydration:
- Soft.A feature of this mode is the gradual increase in temperature in the chamber - due to this property, not only the pristine quality of wood is preserved, but also its natural color. This drying method is the longest.
- Standard. In this mode, the tree retains its pristine strength, while the shade of the material changes slightly.
- Forced. This mode is used if it is necessary to dehydrate raw materials as quickly as possible, however, the quality of lumber is significantly reduced. It is also worth noting that after applying this mode, the tree may darken and acquire a characteristic smell.
We make a drying chamber
So, we figured out what this building is for. Now you can begin to make a dryer for wood with your own hands.
Selection of premises
First of all, you need to correctly choose the room where the lumber will be dried. To do this, follow these tips:
- The area of the premises should be based on the dimensions of the boards that require processing.
- The height of the ceilings should be 2-2.5 meters.
- The width of the room is selected by the user, however, it is worth considering that you need to leave space for a person to pass.
- The windows in the room must be laid with bricks.
- Doors should be such that raw materials can be loaded into them without problems.
- There should be a window or a small air vent for ventilation.
Important! If a large room is chosen, it is better to make a partition for thermal insulation.
Dryer Construction
Usually, a garage or a barn is chosen as a room for a dryer, but sometimes they can’t even be used. For this reason, it is important to know how to make a wood dryer yourself, using the drawings:
- Lay the foundation for the entire structure. Since the mass of the structure will be low, the foundation does not have to be deep.
- After the concrete has dried, it is necessary to assemble the frame from a galvanized steel profile (you can replace it with an aluminum frame). Connect the frame parts using bolts, as well as special brackets.
Important! The aluminum frame is distinguished by its high price from steel, however, it has many advantages. For example, it is much more stable and not afraid of corrosion.
- Sheathe the walls with the roof with steel sheets fixed to the frame using special screws. In order for the effect to be as effective as possible, it is necessary to double cladding, laying a layer of mineral wool insulation with a thickness of about 150 mm between two sheets.
- Lay the waterproofing membrane on the floor, then fill it with sawdust.
- Install the door. They should be closed as tightly as possible.
- Install ventilation ducts or vents to allow air to circulate freely.
- When the work is completed, check the tightness of the room. If necessary, eliminate the mistakes made.
- Equip a do-it-yourself infrared wood dryer This item should be given due attention.
Equipment
Instructions for design equipment may vary. This is due to the fact that the configuration of the camera and the material budget for each user are different.
Consider the general scheme of the equipment of the room:
- Make a support on which a stack of boards will be placed in the future. To do this, you need to fix wooden structures on the floor, which allow you to raise the material approximately 20 cm above the ground. This is necessary to circulate the air flow from below.
- It is possible to use wall racks as supports. To do this, you need to fix metal brackets on the bearing surfaces, which are designed to stack piles along the walls of the chamber.
- Install the heating device. An oven, a heat fan, a fireplace, a heat gun and other facilities can play its role - the choice depends on your desires and preferences.First of all, you need to pay attention to the power of the device - it is calculated from the volume of loaded lumber.
- Install do-it-yourself fans for drying boards. Devices will provide movement to thermal air. Of course, you can get by with a conventional hood, but then the drying time of the raw materials increases several times, which means that the cost of electricity increases.
- Position the fans and air heaters so that the heated air passes across the air stream. Thus, you will reduce the aerodynamic system drag, as a result of which the dryer will work more efficiently.
Important! Since you need a lot of electricity, it is recommended to install a separate power cable for the design. In addition, all the materials that you use must be connected to the distribution panel via an RCD with the required power parameters. This is necessary in order to protect yourself from a possible fire.
If possible, you can install an automatic system that controls the temperature and ventilation of the dryer. This system provides high-quality drying of wood, so its high cost is justified.
to contents ↑Construction use
If you followed all our recommendations and built a drying chamber for wood with your own hands, without making any mistakes, then its use will be very simple and effective. For this:
- You just need to lay the boards in a stack, laying between the rows of bars having a thickness of about 20 mm, then load the stack into the room.
After that, you can change the temperature, gradually raising it.
Important! There are a lot of schemes, following which you can make a competent drying, but inexperienced users are better off using the low temperature mode first. This is due to the fact that its use is accompanied by a minimum number of defective boards.
Consider the classic wood drying process:
- The temperature must be raised to 50 degrees, with a rate of rise of 6 degrees per hour.
- This temperature must be maintained for 5 hours.
- During drying, the moisture content in the tree must be reduced from 30 to 7-8%, for this it is necessary to withstand a temperature of 60 degrees for about two days. At the same time, both the supply and exhaust ventilation must be kept at half the power.
- To condition the room, you need to withstand the boards at a 60-degree temperature using actively working ventilation.
- The tree should cool down without heating and ventilation. Ultimately, you get boards suitable for further work.
Stock footage
From this article, you learned that making a wood dryer with your own hands is not so difficult, but for this you need to spend quite a lot of material resources and time. It is worth noting that all these costs justify their result, because in the end you get much more dried boards than if you bought finished lumber from the manufacturer.
- How to choose a vacuum cleaner taking into account the characteristics of the house and coatings?
- What to look for when choosing a water delivery
- How to quickly create comfort at home - tips for housewives
- How to choose the perfect TV - useful tips
- What to look for when choosing blinds
- What should be running shoes?
- What useful things can you buy in a hardware store
- Iphone 11 pro max review
- Than iPhone is better than Android smartphones