DIY long burning boiler
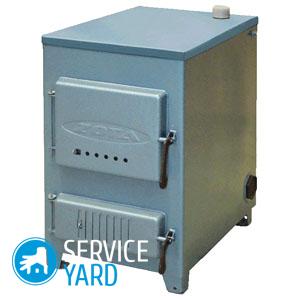
Solid fuel boilers today are one of the most popular and economical ways of heating a household, residential or other type of room. To save money, you can assemble a long-burning boiler yourself. Unfortunately, not everyone has the opportunity to purchase expensive and high-quality equipment, so many "jack of all trades" are looking for a way to make the unit at home. In our article, we will describe the principle of operation of such a device, design features and the algorithm for self-production of a heating unit.
to contents ↑Varieties of boilers
In specialized stores and construction hypermarkets a huge selection of these products is presented. All existing models of solid fuel boilers can be divided into three groups:
- Classic.
- Pyrolysis.
- Pellet.
This is not a complete list of classifications, but the main determining factor in the choice is precisely the principle of fuel combustion. Next, we will consider in more detail the main points of the drawing of a self-made solid fuel boiler of long burning.
to contents ↑Classic boiler
If you look at a classic boiler constructively, it is very similar to a standard furnace. Due to the smaller volume of the combustion chamber, the fuel burns more slowly. In most cases, it is such solid fuel boilers of long burning that many craftsmen make with their own hands.
Design features:
- The design of this type of boiler is quite simple. An automatic draft regulator is located at the top of the boiler, followed by an air heating chamber.
- The next chamber is a switching flap and a telescopic tube; below is a complete combustion chamber and an air distributor.
- A little lower is the combustion and generation zone, and the final zone is fuel.
Important! Structurally, the long-burning boiler circuit is quite simple to manufacture and very convenient with the ability to connect a second circuit to produce hot water.
On how to assemble a solid fuel boiler with long burning with our own hands, we will discuss later in our article.
to contents ↑Water loop pyrolysis boiler
In a device of this type, fuel burns much more slowly, and much less air is required for combustion. Due to this, an additional amount of gas is formed, and in the process of its repeated combustion, the boiler efficiency increases by 85-90%.
For some, it may seem that it is impossible to make a boiler for long burning on wood with a water circuit yourself, but after reading the drawing of the pyrolysis unit you will see the opposite.
Design features of the device:
- The diagram of the drawing is arranged as follows: at the top of the boiler, as in the previous version, there is a chamber for loading fuel.
- The next section is for placing firewood, then there is a special door for igniting and cleaning the boiler.
- At the very bottom of the unit, a pipe with a shutter for supplying primary air and a final ash chamber are placed.
- Parallel to these compartments with fireclay chamotte brick, lay a chamber in which an additional pipe for supplying secondary air is installed, and mount a special door for cleaning.
Important! Fireclay bricks also produce finishing sections of the main combustion of fuel.
- Hot gases are generated in the next compartment, which escape through a specially installed pipe, and a door is also mounted for cleaning the pipe.
to contents ↑Important! The pyrolysis boiler has a water circuit along the entire height of the apparatus.
Pellet boiler
Pellet boilers are rightfully considered the most effective for heating a room.
Thanks to the automated fuel supply process, the efficiency of the device rises to 95%. The auger loaded into a special compartment is automatically poured into the combustion chamber.
to contents ↑Important! Due to the complex design, making a long-burning boiler at home is quite difficult.
Combined boiler
In order for the heating in the room to be of high quality, and most importantly - cost-effective, it is recommended to install a universal boiler that works effectively on any type of fuel.
If you decide to use a device with this principle of operation, then pay attention to combined boilers - they work on alternative types of fuel, and besides, switching modes in such units is quite simple. It is for this reason that many try to make a long-burning boiler with their own hands.
In turn, combined boilers are also divided into some groups:
- Solid fuel combos.
- Universal - any type of fuel is suitable for heating.
- Electric combos.
Types of fuel
At the moment, the question of which fuel to use for solid fuel boilers for long burning is not very relevant. The modern market offers a lot of options for heating the premises, while everyone can choose their own, based on their own financial capabilities:
- Firewood of different species of wood can be presented in the form of compressed coniferous or deciduous sawdust.
- Granular biopellets, compressed sawdust, agricultural waste or peat.
- Coal - you can use any kind of it, regardless of the boiler system, as well as anthracite and fractions.
- Waste from a private woodworking enterprise or agricultural production.
How to make a long-burning boiler at home?
Before you start work, you need to find out the principle of its operation and the sequence of arrangement of all elements.
The principle of operation of the boiler is based on the fact that cold air enters from below through a special chamber. Passing through the warm walls of the boiler, it heats up, rises up and heats the room.
Important! A long-burning boiler has a slightly different principle of operation: the air supply in this case should be minimized in order to increase the duration of combustion. Fuel is loaded as densely and more as possible.
Necessary materials
To assemble a solid fuel boiler of long burning with your own hands, you need to prepare the following components for the device in advance:
- Sheet metal with a thickness of 0.5 to 0.8 mm.
- A pipe with a diameter of 0.3-0.5 cm.
- Metal corners and fittings.
- Gas cylinder with a diameter of 25 cm or a metal pipe.
- Welding machine and electrodes.
- Bulgarian.
Procedure:
- First of all, they collect the controller of air intake into the unit. To do this, a large diameter bolt must be welded to the prepared pipe by welding.
- A circle corresponding to the diameter of the pipe is cut out from a sheet of metal with a grinder. From one edge of the resulting shutter, you need to cut a hole so that the welded bolt passes freely into it.
- Put on the resulting cap and fix it on the pipe with a nut.
Important! The metal circle in the finished product will allow you to control the air supply.
- Next, horizontal holes are cut through the grinder on the pipe, through them air enters the furnace.
- Take a metal sheet and cut out of it another circle with a diameter of 0.5-1 cm less than the diameter of the proposed furnace.
- A hole is cut in the center of the workpiece, into which you need to insert a pipe with a damper and weld at a distance of 20-30 cm from the end.
- Next, you can proceed to assembly of the housing. For this, if a gas cylinder is used, its upper part is removed, if the cylindrical pipe of the corresponding diameter, the bottom is sealed by welding. After that, you can begin to manufacture a chimney.
- A hole with a diameter of 10 cm is cut out in the upper part of the metal cylinder using a grinder, while retreating from the edge exactly the same distance, a thick-walled pipe is welded.
- During the installation of the air supply pipe, a hole is cut through the bottom of the furnace and the pipe is installed in such a way that the blower extends beyond the boiler body.
Important! For normal air circulation inside the boiler, the air supply pipe is located slightly below the chimney.
- The next step will be the manufacture and installation of heat dissipation screen. For this, a circle with a diameter of 20-22 cm with a thickness of at least 10 mm is cut out of a sheet of metal. For ease of use, a handle is welded from the fittings.
- A convection casing is made from a sheet of metal, for this a circle is cut with a diameter larger than the furnace by 5-7 cm.
- By means of welding, the convection chamber and the base of the stove are fixed between themselves.
- The final stage in the process of manufacturing a long-burning boiler is the production of the top cover. If you used a gas bottle as the basis, you can use the upper previously trimmed part. If the base was a sheet of metal, a circle of the corresponding diameter is cut out.
Important! For ease of use, handles from fittings are welded to the upper part.
- To ensure proper air circulation, legs or an additional support with a height of 25-30 cm are welded to the bottom of the boiler in the appliance. Metal corners or a channel are perfect for this.
to contents ↑Important! The safe operation of a solid fuel boiler with long burning is ensured by a high-quality housing. Based on this, heat-resistant thick-walled steel with a thickness of at least 5 mm is used for its manufacture. Remember, the thicker the walls of your boiler, the longer it will retain heat.
Stock footage
This article provides basic information on how to make a long-burning boiler. In order to qualitatively and reliably carry out the entire process of work, you will need correctly drawn up drawings, quality materials and a little patience. As a result, you will get an economical, inexpensive system for heating a room that will last you more than a dozen years.
- How to choose a vacuum cleaner taking into account the characteristics of the house and coatings?
- What to look for when choosing a water delivery
- How to quickly create comfort at home - tips for housewives
- How to choose the perfect TV - useful tips
- What to look for when choosing blinds
- What should be running shoes?
- What useful things can you buy in a hardware store
- Iphone 11 pro max review
- Than iPhone is better than Android smartphones