DIY concrete staircase
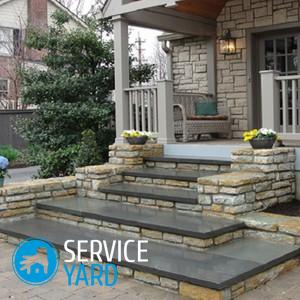
The staircase is a complex architectural structure. It must be reliable, safe, aesthetic and comfortable. Of course, I want her to serve as long as possible, while she did not have to be repaired. Therefore, a concrete staircase with your own hands is a worthy option. This material is expressive from an artistic point of view, it lasts a long time, and you can work with it yourself without the help of professionals.
to contents ↑Material Features
Concrete is a popular material. It is used to produce a wide variety of designs. If you take into account the degree of reliability, then here this material will not be equal. The advantages of this material are:
- Strength and durability;
- Uniform load distribution due to the fact that reinforcement is used;
- Resistance to temperature and moisture;
- Monolithicity;
- A variety of decorative solutions;
- Good combination with a variety of materials.
to contents ↑Important! If technology is not followed, flaws may appear. For instance:
- if you use low-quality raw materials and violate the ratio of strength and load, cracks may appear in concrete, it will crumble;
- if the room is high humidity, a fungus may appear;
- if you do not do additional decoration, the appearance of the coating will be gray and nondescript.
Types of concrete stairs
Systems of this material are presented in two types:
- Capless;
- Combined.
What is good monolithic concrete staircase? This is a common installation that can be applied anywhere. But the combined staircase is a complex metal structure that acts as a frame for fixing concrete steps. To cast them, they use formwork with a reinforcing mesh.
to contents ↑Important! To make steps, use a mixture of concrete, granite crushed stone and marble chips. When the concrete mix dries, the surface is polished.
Subtleties of design and calculation:
- To make the work easier, you can use your own sketch.
- The first step is to determine what position the staircase will be in. It can be located on the ground, next to the wall, to connect two opposite walls, etc. All these indicators affect the further calculations and installation of the structure.
- When calculating the stairs, be sure to consider what size the steps will be and in what quantity. Usually they recommend a height of 160-200 mm, a width of at least 270 mm. If in the end, after all the calculations, it turns out that the number of steps exceeds fourteen, then it is better to divide them into two spans.
Important! Be sure to consider the needs of people living in the house. Older people have difficulty climbing high stairs. But if there are small children, they can hit the step.
- When designing a staircase, be sure to consider that the angle should vary from 24 to 45 degrees. The higher the angle of inclination, the more difficult it will be to climb stairs.
- You should consider the width. It should not be more than 800-900 mm.
- When formwork materials are selected, it takes into account how much the entire structure will weigh.
Important! If the concrete thickness is 200 mm, then a square meter will weigh about five hundred kilograms. At the same time, the weight of a meter march with a length of 4 m will be more than 2.5 tons.
- To get a high-quality concrete mortar, it is better to use a concrete mixer. To make a concrete staircase with your own hands turned out to be of high quality, the solution is compacted using a special electric vibrator.
Important! The better the solution is, the more solid the base will be.
- In order to prevent the surface from drying out after pouring, it is covered with a film of polyethylene. The formwork is removed after about a month, when the concrete becomes strong.
We assemble the formwork
Even a spiral staircase made of concrete with their own hands can not do without the construction of formwork:
- Most often, it is made from materials based on wood. For the manufacture of supports and racks, they use 100x100 mm timber, for the formation of steps - edged or semi-edged boards, the thickness of which is at least 30 mm, for curved parts they use plywood or OSB boards.
- So that the boards do not warp under the influence of moisture, which is in concrete, before reinforcing, laying of waterproofing litter should be done. Here you can use roofing material, plastic wrap or alkyd varnish.
- When assembling the formwork, you need to use self-tapping screws, it is better not to use nails. It is better to take phosphated (black) self-tapping screws having an incomplete thread.
- To connect the parts, use metal corners or wooden short bars.
- To cut wood materials, use an electric jigsaw.
to contents ↑Important! When installing kits, be sure to consider that concrete weighs a lot. Racks should not hang in the air. If necessary, wedges or pads are installed. To increase the rigidity of the structure, the racks are connected using boards.
Reinforcement cage
To make the whole structure more durable and rigid, reinforcement is performed. In this case, ribbed reinforcement with a diameter of 10-12 mm is used. A soft wire is used to bundle individual parts.
to contents ↑Concreting
Concrete is poured in one go. The air temperature should be positive. The first step is to fill the lower steps.
Important! To avoid leakage of concrete, crushed stone of 10-20 mm is added to it.
In order to prevent air cavities in the concrete, it must be densified with an electric vibrator. It is important not to touch the fittings, since in this case it will be worse to bond with the fittings.
In order to make concrete, prepare a mixture of:
- Cement grade M 400, one part;
- Sand, two parts;
- Crushed stone, four parts;
- Water, 600 ml;
- Plasticizer, 10 ml.
Then we adhere to such a scheme of work so that the concrete staircase with our own hands is of high quality:
- A concrete mixer is used to mix the components.
- After pouring, the wet mass is covered with a film so that it does not crack upon rapid drying.
- Formwork dismantling is carried out only after four weeks.
- After gaining concrete strength, the march is finished and the fence is installed.
to contents ↑Important! To avoid unnecessary workload, experts recommend using wood as a finish. Wood can be used both for the manufacture of steps, and for handrails with balusters. Ceramic tiles are also used to finish the steps. In addition, it is possible to use clean concrete surfaces, which are coated with a protective compound and sanded.
Stock footage
Now you know how to make a concrete staircase. To make the stairs, you will have to spend a lot of time and effort, but even a beginner can handle this, if desired.
- How to choose a vacuum cleaner taking into account the characteristics of the house and coatings?
- What to look for when choosing a water delivery
- How to quickly create comfort at home - tips for housewives
- How to choose the perfect TV - useful tips
- What to look for when choosing blinds
- What should be running shoes?
- What useful things can you buy in a hardware store
- Iphone 11 pro max review
- Than iPhone is better than Android smartphones